BMW macht Modellpflege. So kann der elektrische BMW iX ab März 2023 wie auch die Luxus–Limousine BMW i7 manuell die Batterie vorheizen (vorkonditionieren). Warum ist das wichtig? Bislang ermöglichen die meisten Autohersteller nur eine automatische Vorkonditionierung. Dabei werden die Batteriezellen rechtzeitig vor einem Ladestopp in das richtige Temperaturfenster gebracht. In der Regel müssen sie erwärmt werden. Dann startet das Fahrzeug direkt mit einer hohen bzw. der maximal möglichen Ladeleistung am Schnelllader. Der Ladestopp verkürzt sich, man ist schneller wieder unterwegs. Vorkonditionierung ist also vor allem in der kalten Jahreszeit ein wichtiges Thema.
Kürzerer Ladestopp mit Vorkonditionierung
Allerdings funktioniert das bei den meisten Anbietern nur, wenn der Ladestopp im Navi hinterlegt ist. Nur dann weiß das System, wann es mit dem Vorheizen beginnen muss. Für meine Tour mit dem Ioniq 5 in norwegische Tromsö war das extrem hilfreich. ABER: Ist bei dem Modell die Ladesäule als Ziel im Navi hinterlegt, funktioniert die Vorkonditionierung nicht. Kennt das Navi die Ladesäule nicht, weil die gerade erste ans Netz gegangen ist, klappt es auch nicht. Wer zu seiner “Stammladesäule” fährt, macht sich nicht die Mühe, das Navi zu nutzen. Was fehlt: Ein Knopf bzw. ein Menüpunkt im System, mit dem man manuell die Batterie vorkonditioniert. Genau das liefert nun BMW. Hut ab. Warum die anderen Hersteller da so zögerlich sind, erschließt sich mir nicht. Bei meinem Polestar 2 wird die Vorkonditionierung nicht mal im Display angezeigt. Ich muss mich als Fahrer darauf verlassen, dass es funktioniert.
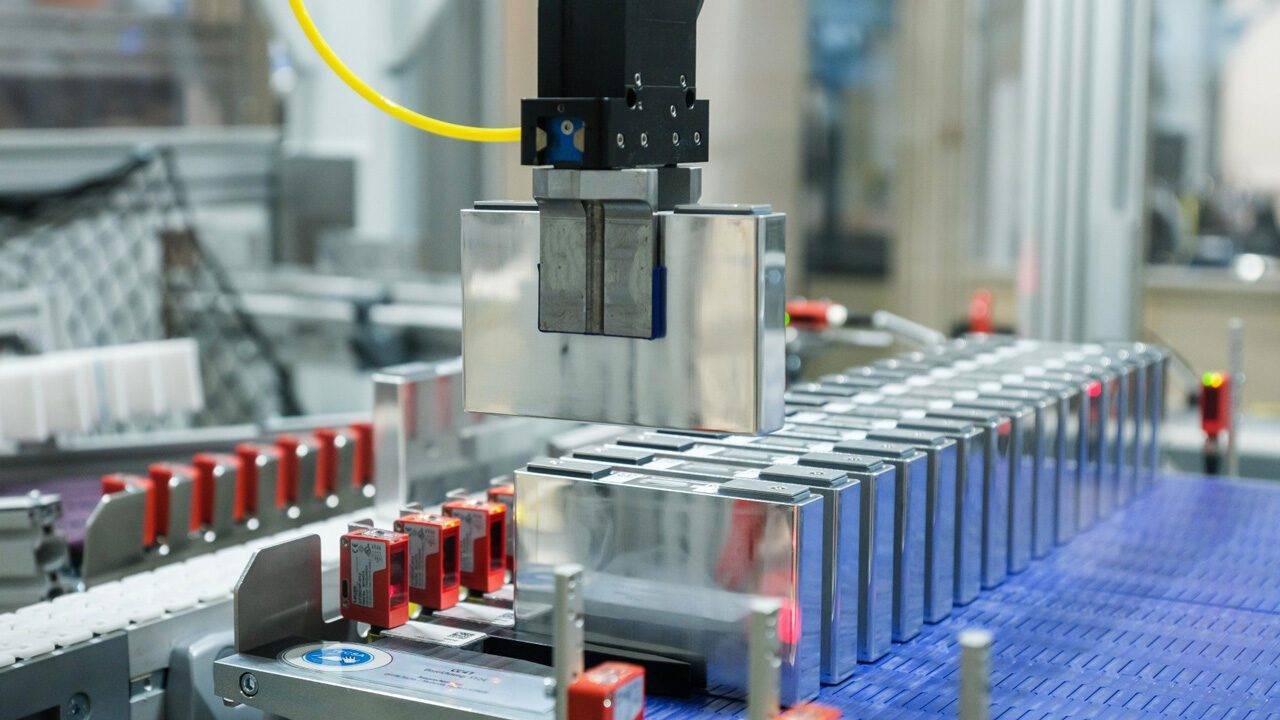
Werk Leipzig setzt auf Batterien
Die erste Produktionsanlage für die Zelllackierung ist im BMW Werk Leipzig in den Serienbetrieb gegangen. Sie nimmt 2.300 m² Fläche in der ehemaligen Produktionshalle für den BMW i3 ein, dessen Produktion im Sommer vergangenen Jahres endete. Zusätzlich zu den zwei bestehenden Fertigungslinien für Batteriemodule und der Lackieranlage für Batteriezellen kommen bis April 2024 eine weitere Batteriemodullinie, vier Zelllacklinien und zwei Montagelinien zur Fertigung von Hochvoltbatterien hinzu. „Ab 2024 werden wir am Standort Leipzig die gesamte Prozesskette der Hochvoltbatteriefertigung abbilden können“, sagt Markus Fallböhmer, Leiter Batterieproduktion bei der BMW Group. Ziel der BMW Group ist, bis 2030 mindestens die Hälfte des Absatzes mit vollelektrischen Fahrzeugen zu erzielen.
Warum werden Batteriezellen lackiert?
Die Anlage kann mehr als zehn Millionen Zellen pro Jahr lackieren und schafft pro Stunde über 2.300 Zellen. Die Lithium-Ionen-Zellen werden zunächst mit einem Laser vorbehandelt und strukturiert. Ein Laserstrahl „meißelt“ eine Struktur in die unlackierte Zelle, um die Oberfläche zu vergrößern und die Oberflächenspannung des Aluminiumgehäuses zu reduzieren. Die anschließende Plasmareinigung entfernt Schmutzpartikel und Oxide. Beide Verfahren dienen der besseren Lackhaftung. Die Zellen werden anschließend in einer Anlage in zwei Schichten lackiert und UV gehärtet. Der Lack sorgt für eine optimale Isolierung der Zellen. Bei der BMW Group werden die Zellen blau lackiert. Die Farbe wurde bewusst gewählt, da blau für die Positionierung und als Akzentfarbe der BMW i Elektrofahrzeuge eine bedeutende Rolle spielt.
Nach der Zelllackierung werden die Batteriezellen zu einer größeren Einheit, den sogenannten Batteriemodulen, zusammengefügt. Die fertigen Batteriemodule werden anschließend gemeinsam mit den Anschlüssen zum Fahrzeug, Steuergeräten und Kühlaggregaten in ein Aluminiumgehäuse montiert.
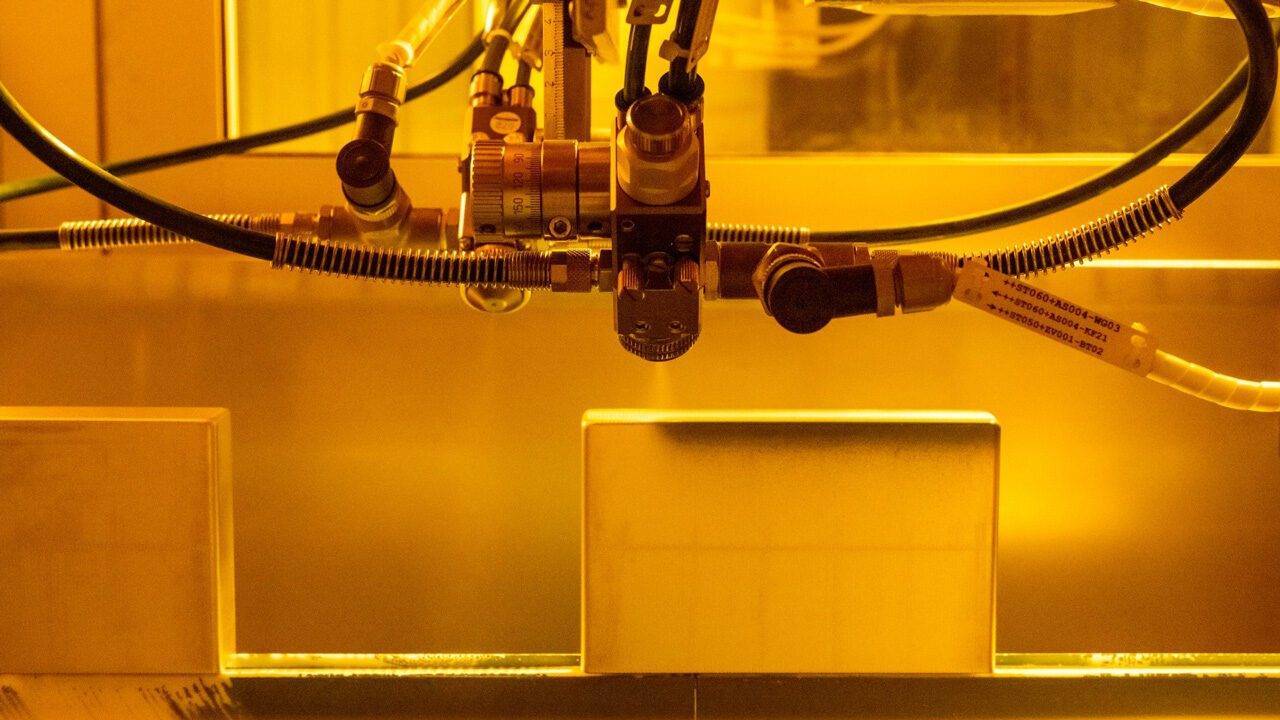
Zukunftsfähigkeit des Leipziger Werks sichergestellt
Die E-Komponentenfertigung ist Impulsgeber für den weiteren Ausbau des Leipziger Werks. Künftig werden E-Komponenten auf einer Fläche von rund 150.000 m² produziert. „Das ist eine nachhaltige Investition in die Zukunftsfähigkeit des Leipziger Werks“, sagt Werkleiterin Petra Peterhänsel, „Derzeit sind bereits mehr als 800 Mitarbeiterinnen und Mitarbeiter in der E-Komponentenfertigung am Standort Leipzig tätig, bis 2024 werden es mehr als 1.000 sein.“
Ein nächster großer Meilenstein für das Werk ist die Produktion des MINI Countryman Nachfolgers, der ab Ende 2023 in Leipzig vom Band rollen wird. Das Crossover-Modell wird sowohl mit Verbrennungsmotoren als auch reinem Elektro-Antrieb angeboten werden.